Il est indéniable que qu’est-ce qu’un automate constitue la pierre angulaire de l’automatisation industrielle moderne. Mais comment fonctionne exactement cette technologie ? Dans cet article, nous approfondissons l’essentiel des automates, offrant une explication claire de leur rôle et de leurs mécanismes dans le contexte plus large des processus industriels.
Qu’est-ce que l’automate ?
Un automate programmable (PLC) est un dispositif informatique spécialisé conçu principalement pour être utilisé dans les environnements d’automatisation industrielle et de fabrication. Il contrôle efficacement divers processus électromécaniques basés sur des entrées programmables et des règles spécifiques définies par l’utilisateur.
Cette technologie permet une gestion précise des machines et des chaînes d’assemblage, garantissant l’efficacité opérationnelle et la fiabilité des tâches qui nécessitent une haute précision et des actions répétitives.
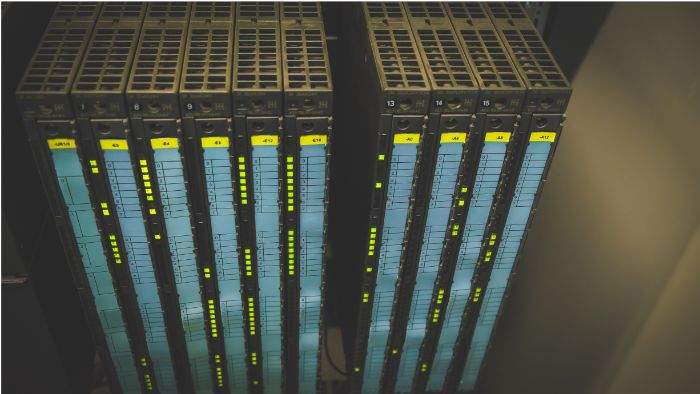
L’histoire du PLC
Engineer Richard E. “Dick” Morley is often referred to as the father of the PLC. In 1968, he developed the first semiconductor-based solution he called the “Modicon” (MOdular Digital Controller). It was designed to replace hardwired relay systems which had a tangle of wires and were consequently difficult to update and maintain.
Avec leur introduction, les automates ont considérablement réduit le temps, les coûts et les efforts nécessaires à la mise à jour et à la modification des processus de production. Cette innovation a non seulement simplifié l’infrastructure physique des systèmes de contrôle en éliminant un câblage important, mais a également introduit un niveau plus élevé de flexibilité dans la conception du système.
En conséquence, l’automatisation industrielle est devenue plus rationalisée et efficace, facilitant une meilleure communication entre les appareils et permettant des opérations plus complexes et adaptables.
Avantages du contrôle numérique avec automates
Contrairement aux contrôleurs électromécaniques, la programmation des API est entièrement numérique, ce qui signifie qu’un API est capable de gérer des tâches de contrôle beaucoup plus complexes. Si des ajustements ou des améliorations sont nécessaires, le programme existant peut simplement être modifié ou complètement réécrit.
De plus, une fois qu’un programme est développé, il peut être dupliqué, utilisé de manière répétée et amélioré par des commentaires complets et une documentation approfondie. Cet aspect simplifie grandement le processus de modification et de mise à jour des programmes à tout moment ultérieur, faisant des automates un outil incroyablement polyvalent dans l’automatisation industrielle.
Cette approche numérique élimine le besoin de recâblage manuel et réduit le risque d’erreurs, rationalisant ainsi considérablement les processus de dépannage et de maintenance.
Composants d’un automate
Un automate est composé de plusieurs composants clés qui permettent sa fonctionnalité :
- CPU (unité centrale de traitement) : agit comme le cerveau de l’automate, traitant toutes les données des entrées pour exécuter le programme de contrôle et envoyant des commandes aux sorties.
- Entrées : ce sont des interfaces telles que des capteurs qui fournissent des données en temps réel à l’automate concernant les conditions de fonctionnement.
- Programme : ensemble d’instructions écrites par l’utilisateur qui dicte la manière dont l’automate doit fonctionner en fonction des entrées reçues.
- Sorties : composants tels que des actionneurs ou des relais qui mettent en œuvre les décisions prises par le processeur de l’automate.
La fonctionnalité de l’automate
Le fonctionnement d’un automate programmable (PLC) implique plusieurs étapes clés qui garantissent un contrôle et une automatisation efficaces :
- Détection des états des périphériques d’entrée : L’automate surveille en permanence l’état des différents périphériques d’entrée qui lui sont connectés.
- Entrées discrètes : ces entrées représentent des états binaires, tels que marche/arrêt, 1/0, ouvert/fermé. Des exemples d’entrées discrètes incluent un interrupteur à bouton-poussoir, qui peut être activé ou désactivé, ou une vanne, qui peut être ouverte ou fermée.
- Entrées analogiques : contrairement aux entrées discrètes, les entrées analogiques signifient des données sur un continuum de valeurs. Ils sont essentiels pour mesurer des variables telles que la température, la pression, les niveaux de dioxyde de carbone ou le poids. Par exemple, un capteur de température peut enregistrer une plage continue de température allant du point de congélation au point d’ébullition.
- Exécution des instructions du programme : Sur la base des données reçues de ces entrées, l’automate traite et exécute les instructions du programme prédéfinies. Cette programmation détermine la façon dont l’automate répond aux différentes conditions d’entrée, permettant une automatisation dynamique et réactive.
- Fonctionnement des périphériques de sortie : suite à l’exécution de son programme, l’automate envoie des signaux aux périphériques de sortie pour effectuer des actions basées sur les entrées et la logique du programme.
- Des exemples de périphériques de sortie incluent les alarmes, qui peuvent retentir dans des conditions spécifiques ; des voyants lumineux, qui fournissent un retour visuel ; des vannes qui contrôlent le débit de fluide ; et des affichages visuels, qui affichent les états ou les alertes du système.
Applications
Applications des automates dans la vie quotidienne
Les automates programmables (API) sont profondément intégrés dans divers aspects de la vie quotidienne, fonctionnant souvent en coulisses pour améliorer l’efficacité et la sécurité à notre insu.
- l’éclairage des rues: L’une des applications les plus visibles des automates est la gestion de l’éclairage public. Le contrôle de ces systèmes aide les villes à économiser beaucoup d’énergie et à réduire leurs coûts, car l’éclairage public peut consommer une part substantielle du budget des services publics d’une ville, représentant parfois 35 à 45 % des dépenses totales.
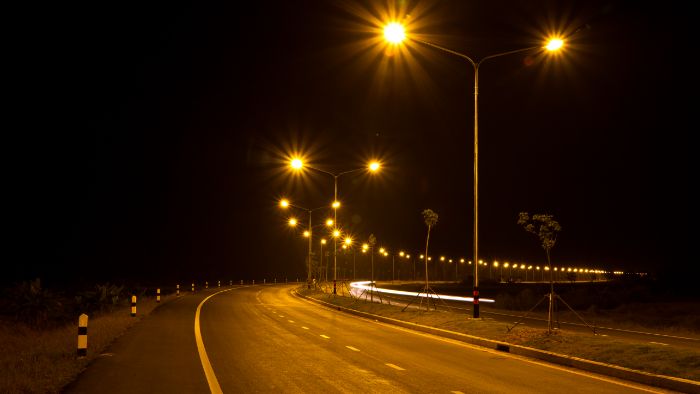
Grâce aux systèmes intelligents basés sur des API, les dépenses en matière d’éclairage public peuvent être réduites jusqu’à 70 %. Ces systèmes utilisent des données en temps réel telles que l’heure de la journée, le retour des capteurs de lumière et la détection des piétons ou des véhicules pour optimiser le moment où les lumières sont allumées ou éteintes.
Applications quotidiennes supplémentaires :
- Circuits de feux de circulation : les automates gèrent la séquence et la synchronisation des feux de circulation, améliorant ainsi la fluidité et réduisant les embouteillages.
- Affichage numérique : ces panneaux modifient le contenu de manière dynamique, en utilisant des automates pour des mises à jour et des ajustements en temps opportun.
- Systèmes automobiles : dans les véhicules, les automates sont utilisés pour contrôler les essuie-glaces électriques et les pompes d’injection de carburant, en adaptant leur fonctionnement en fonction des conditions de conduite.
- Domotique : cela comprend les volets à commande automatique, les systèmes de contrôle du chauffage et les systèmes de portail, qui s’ajustent en fonction des entrées environnementales et des préférences du propriétaire.
- Transport vertical : les ascenseurs et les escaliers mécaniques utilisent des automates pour un contrôle précis des mouvements, garantissant ainsi la sécurité et l’efficacité de leur fonctionnement.
Le rôle des automates dans la fabrication industrielle
Dans le domaine de la fabrication industrielle, l’avènement des automates programmables (PLC) a révolutionné la façon dont les processus sont surveillés et contrôlés. Ces systèmes électroniques basés sur la logique sont indispensables pour automatiser des tâches de fabrication complexes, réduisant ainsi considérablement les délais, les coûts et la main d’œuvre.
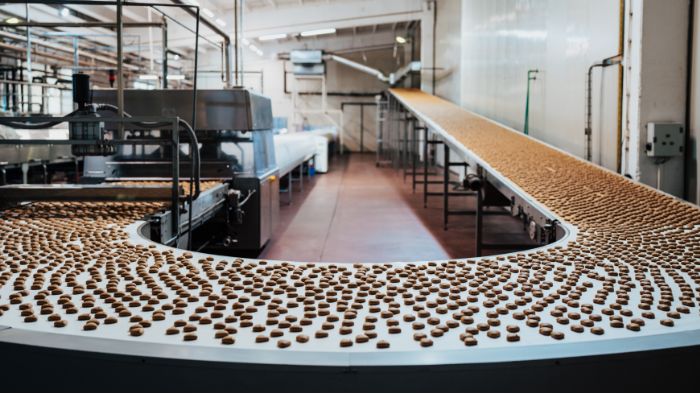
Exemple dans les opérations de l’industrie agroalimentaire :
Une application pratique des PLC se trouve dans le secteur de la production alimentaire. Par exemple, lors de la fabrication de chips, un automate peut jouer un rôle essentiel dans le contrôle de la qualité. Voici comment fonctionne généralement le système :
- Détection d’entrée : des capteurs de lumière installés le long de la bande transporteuse servent de dispositifs d’entrée pour l’automate. Ces capteurs détectent la couleur de chaque chips passant sur le convoyeur.
- Traitement logique : sur la base des données des capteurs de lumière, la logique du programme de l’automate détermine le moment exact et l’activation de ventilateurs spécifiques. La logique est programmée pour identifier les puces plus sombres et probablement brûlées.
- Activation de la sortie : Une fois qu’une puce brûlée est détectée, l’automate active des ventilateurs ciblés à des endroits précis le long de la bande. Ces surpresseurs permettent d’évacuer les copeaux brûlés de la ligne de production, préservant ainsi la qualité du lot.
Autres applications industrielles :
- Opérations robotiques : dans la fabrication automobile, les automates contrôlent les robots qui effectuent des tâches telles que le soudage et l’assemblage de pièces, améliorant ainsi la précision et la vitesse.
- Lignes d’assemblage : les automates synchronisent le fonctionnement des bandes transporteuses et des machines pour optimiser le processus d’assemblage, comme dans la fabrication de produits électroniques. Notre entreprise est spécialisée dans le développement d’étiqueteuses et dispose de nombreuses solutions d’étiquetage, telles que solutions d’étiquetage de seringues et solutions d’étiquetage inviolables, qui utilisent des automates pour obtenir une efficacité d’assemblage accrue.
- Fonctions des machines : dans la fabrication textile, les automates régulent le fonctionnement des métiers à tisser et autres machines, en ajustant les paramètres pour différents types et conceptions de tissus.
Intégration d’automates dans les systèmes SCADA
Les contrôleurs logiques programmables (PLC) sont généralement intégrés en tant que composants cruciaux des systèmes de contrôle de surveillance et d’acquisition de données (SCADA). Ces systèmes décentralisés sont conçus pour surveiller, visualiser et contrôler les opérations dans des environnements industriels, les API et les unités de terminaux distants (RTU) gérant la majorité de ces tâches de contrôle.
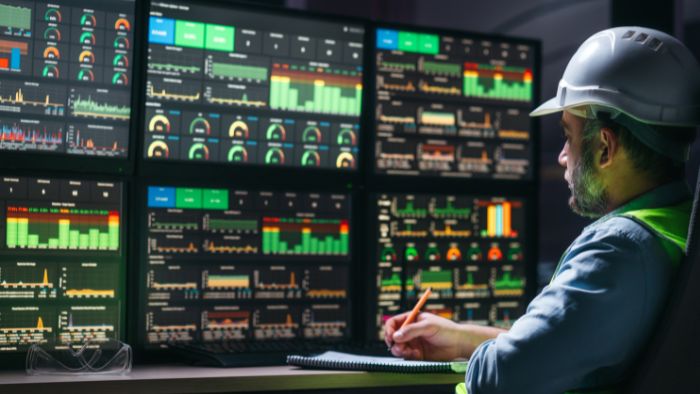
Processus de collecte de données et d’interaction :
- Collecte de données : le processus commence par la collecte par les automates des données provenant de diverses machines sur l’atelier de production. Ces contrôleurs servent d’interface principale pour l’acquisition de données en temps réel, collectant des informations sur les paramètres opérationnels et l’état de la machine.
- Visualisation et interaction des données : après la collecte, ces données sont relayées vers des interfaces homme-machine (IHM), qui visualisent les informations pour les opérateurs. Les IHM jouent un rôle essentiel en rendant les données complexes compréhensibles, permettant aux opérateurs de voir les tendances et de recevoir des alertes.
- Interaction du logiciel SCADA : les opérateurs interagissent avec le système SCADA via des plates-formes logicielles telles que Ignition. Ce logiciel permet une analyse sophistiquée des données, une gestion du système et une aide à la prise de décision en fournissant des outils pour manipuler et approfondir les données collectées par les automates.
Capacités système étendues :
- Surveillance et contrôle à distance : au-delà du contrôle local, les systèmes SCADA permettent la surveillance et le fonctionnement des équipements à distance, permettant ainsi de prendre des décisions à partir de salles de contrôle centralisées capables de gérer plusieurs sites.
- Évolutivité et intégration du système : les automates des systèmes SCADA peuvent facilement être mis à l’échelle pour s’adapter à des opérations en expansion ou pour intégrer de nouvelles technologies et équipements, les rendant ainsi adaptables à l’évolution des demandes industrielles.
- Efficacité opérationnelle améliorée : en automatisant les processus de collecte de données et de réponse, les automates réduisent le risque d’erreur humaine, augmentent la vitesse de réponse aux problèmes potentiels et optimisent les processus de production, améliorant ainsi l’efficacité opérationnelle globale.
Différences entre un automate et un ordinateur industriel
Les ordinateurs industriels sont souvent considérés comme le cœur de l’Industrie 4.0, fonctionnant de manière similaire aux automates en termes de réception d’entrées, de production de sorties et de contrôle des processus d’automatisation. Cependant, il existe des différences distinctes entre la façon dont l’automatisation est contrôlée par un automate et par un ordinateur industriel.
Interfaces et connexions
Bien qu’un automate offre une large sélection d’options d’E/S, sa connectivité est généralement plus restreinte par rapport à un PC industriel. Les PC industriels peuvent s’interfacer avec une gamme plus large de périphériques externes, notamment des écrans, des pilotes, des imprimantes, des cartes d’interface réseau et des périphériques de divers fabricants. La flexibilité des différentes options d’E/S et des emplacements pour cartes permet à un PC industriel d’être hautement personnalisable et extensible en fonction des besoins spécifiques.
Par exemple, un PC industriel peut accueillir des améliorations telles que des cartes sans fil ou cellulaires, des interfaces homme-machine (IHM) ou des systèmes de vision, élargissant ainsi considérablement son champ d’application. Néanmoins, pour remplacer entièrement un automate, un PC industriel doit être équipé de la pile logicielle appropriée, garantissant qu’il peut répondre aux exigences spécifiques du contrôle des automatismes industriels.
Performances et stockage
Les PC industriels offrent des performances de processeur supérieures et des capacités de stockage améliorées par rapport aux automates. Ces fonctionnalités offrent des avantages significatifs, notamment dans la gestion d’analyses de données complexes, l’enregistrement approfondi de données et l’intégration de technologies avancées telles que l’intelligence artificielle et l’apprentissage automatique.
De plus, la flexibilité de programmation offerte par les PC industriels leur permet de gérer plus efficacement des scénarios complexes. Un autre avantage des PC industriels est leur capacité à consolider les charges de travail, ce qui est particulièrement précieux dans les environnements où l’espace est limité.
En réduisant l’empreinte matérielle, les PC industriels peuvent optimiser l’utilisation de l’espace physique tout en conservant des niveaux de performances élevés. Cela les rend idéaux pour les applications industrielles sophistiquées où l’efficacité et l’utilisation de l’espace sont essentielles.
Considérations de sécurité
Les automates fonctionnent avec un système d’exploitation dédié très simple, développé spécifiquement pour les tâches de contrôle à accomplir. Cette approche logicielle ciblée et minimaliste tend à minimiser les vulnérabilités de sécurité que l’on retrouve souvent dans les systèmes d’exploitation grand public plus complexes.
D’un autre côté, un PC industriel nécessite un système d’exploitation plus polyvalent pour exécuter diverses applications, ce qui soulève potentiellement des questions sur sa vulnérabilité aux cyberattaques.
Cependant, les PC industriels modernes sont conçus avec des fonctionnalités de sécurité robustes pour atténuer ces risques. De plus, l’utilisation généralisée des PC garantit que les vulnérabilités de sécurité sont identifiées et corrigées rapidement grâce à des mises à jour régulières.
En revanche, les automates sont mis à jour moins fréquemment et s’appuient sur une technologie plus ancienne, ce qui peut conduire à un environnement moins sécurisé au fil du temps. Cette différence met en évidence la nécessité de mesures de sécurité proactives, en particulier dans les applications industrielles critiques où l’impact d’une faille de sécurité pourrait être grave.
Durabilité
Lorsque l’on compare la durabilité des automates programmables à celle des ordinateurs industriels, il est important de noter que les deux sont conçus pour résister aux conditions difficiles généralement rencontrées dans les environnements industriels.
Contrairement aux PC conventionnels, les API et les PC industriels sont conçus pour résister à des températures extrêmes, à la poussière, à l’humidité et aux vibrations, garantissant ainsi des performances fiables même dans des environnements difficiles.
Cette construction robuste est essentielle car elle évite les perturbations opérationnelles et maintient les processus industriels continus.
Perspectives d’avenir
Avec les progrès de la technologie, l’application du PLC dans les domaines de l’automatisation et de la fabrication intelligente deviendra plus étendue et plus approfondie. Les futurs automates pourraient intégrer des capacités de traitement de données plus avancées et des algorithmes d’intelligence artificielle, leur permettant de gérer plus intelligemment des tâches de contrôle complexes et d’analyse de données.
De plus, avec le développement de la technologie Internet des objets (IoT), les automates pourraient être plus étroitement intégrés aux technologies de cloud computing et de big data pour permettre une surveillance et une gestion à distance plus efficaces, améliorant ainsi considérablement l’efficacité et la sécurité de la production.
Dans le même temps, la conception des automates peut accorder davantage d’attention à l’efficacité énergétique et à la protection de l’environnement, conformément aux exigences du développement durable mondial.
Conclusion
En résumé, l’importance de qu’est-ce qu’un automate dans le domaine de l’automatisation industrielle ne peut être surestimé. Ces automates programmables ont remodelé le fonctionnement des industries en offrant un contrôle robuste, fiable et efficace sur des processus complexes.
En permettant une personnalisation étendue, des mises à jour rapides de la programmation et une intégration transparente avec d’autres avancées technologiques, les automates continuent d’être la pierre angulaire du développement de systèmes automatisés qui améliorent la productivité et réduisent les risques opérationnels.
En tant qu’entreprise d’automatisation d’équipements d’étiquetage pharmaceutique, PLC nous aide à améliorer l’efficacité de l’assemblage de nos machines des manières suivantes : en aidant nos étiqueteuses à s’adapter à différents types et tailles d’étiquettes, en obtenant une fixation précise des étiquettes et en détectant et en enregistrant l’état de fonctionnement. et informations sur les défauts des machines à étiqueter.
En plus de l’étiqueteuse inviolable et de l’étiqueteuse de seringues, nous proposons d’autres solutions de machines qui utilisent des automates, comme suit :
Solution d’étiquetage d’ampoules
Solution d’étiquetage pour auto-injecteurs
Solution d’étiquetage de flacons
Solution d’étiquetage des flacons de pilules